ニュース
OKIの作業支援システムがSUBARUのエンジン組み立てをサポート
2019/11/15 20:00
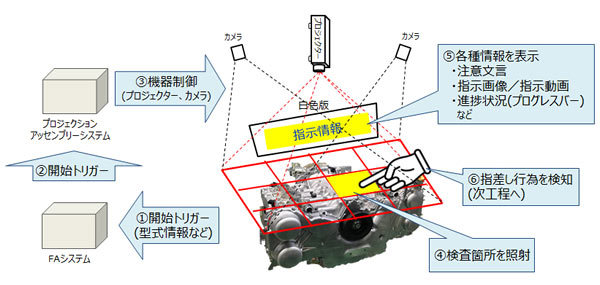
フォレスター、レヴォーグなどのSUBARU車の生産を担う群馬製作所の中で大泉工場は、自動車用エンジン、トランスミッションの製造を行っている。これらの製品は、自動車を構成するパーツの中でも特に高い品質と耐久性が求められており、加工・組立工程の後、外観検査、運転検査などの工程を経て完成車工場へ出荷している。これらの工程では、重要箇所や重要パーツの指差し確認が必要不可欠となっており、SUBARUでは高い品質や精度を保ちながら、作業員の負荷を軽減する仕組みを検討していた。
今回の実証実験では、製造現場で組立作業ナビゲーションとして実績のあるプロジェクションアッセンブリーシステムをSUBARUのFAシステムと連携させ、指差し確認など人が介在する作業を支援するシステムとして活用することを目指している。
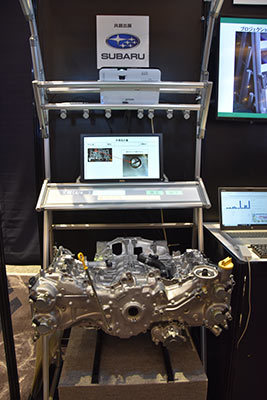
プロジェクションアッセンブリーシステムは、OKIのIoT活用工場ソリューション「Manufacturing DX」による現場変革ソリューションの一つで、プロジェクターによる的確な作業指示を行い、さらに画像センシングにより作業実績をデジタル化することで、現場の作業を支援するシステム。
そのプロジェクションアッセンブリーシステムとFAシステムを連携させることで、指差し確認箇所や作業手順をプロジェクションマッピングにより作業対象のワークそのものに直接投影することができる。これにより作業員は、車種や型式で多数のバリエーションが存在する工程においても、一問一答形式で抜け漏れなく確実に、手順を消化できる。
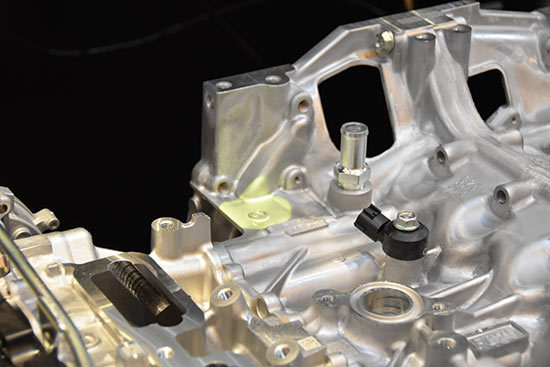
また、作業実績データを取得することで、作業員が作業を実施した証跡となるだけでなく、可視化により「作業時間のばらつき具合」や「作業手順における問題箇所」の特定への活用など、高い品質の維持と作業員の負荷軽減への効果が期待できる。
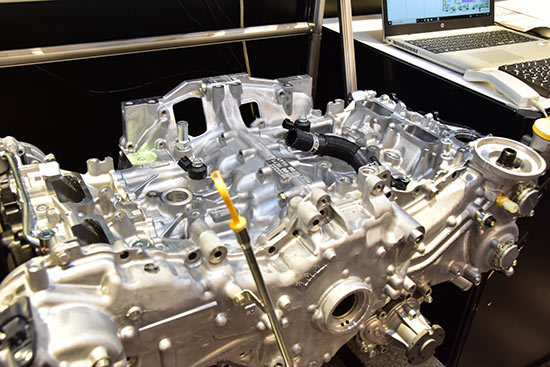
11月14日・15日に開催している「OKIプレミアムフェア 2019」では、プロジェクションアッセンブリーシステムとFAシステムを連携し、エンジンの組み立て作業を支援するPCSを展示した。プロジェクションマッピングにより、作業対象のワークそのものに直接投影するシステムは他社でもあるが、エンジンのような凹凸の多い複雑な形状のもの正確に投影できるようにするため、今後現場でブラッシュアップしていくという。
- 1
関連記事
「OKIプレミアムフェア 2019」が開幕、鎌上社長は「AIエッジに注力」と語る
住友電工、5Gを活用して工場の安全性を高める実証実験、2020年3月から
ネットワン、アドバンス新本社工場のスマートファクトリー環境を構築
シュナイダー、サブスクリプション型のITインフラ設備管理ソリューション